AVR is specialized in processing various types of residual waste and converting this waste into energy and raw materials for households and businesses. In their plant in the Botlek (Rotterdam) they operate a steam turbine which drives a generator. AVR used a Bently Nevada BN3500 overspeed detection system (ODS) to detect overspeed situations and zero-speed.
When an overspeed situation occurs the system should trip the steam turbine to prevent potential damage and dangerous situations. Zero-speed was monitored to prevent the turning gear from starting soon. The turning gear can only be started, when the rotor has come to a complete stop, as this could otherwise damage the turning gear.
Failing BN3500 overspeed cards
AVR contacted Istec because the three overspeed protection cards of their Bently Nevada ODS failed simultaneously. This caused downtime of the process as the steam turbine could not be started up, leaving the generator unpowered.
Initial examination of the application by Istec indicated that the eddy current speed sensors seemed to be working properly. However, the supply voltage showed abnormal values. After checking the log of the Bently Nevada system an error message was found on the 24V power supply, 5V power lines, and 12V power lines. As a result, the output signals were disrupted, causing the overspeed protection cards and zero-speed card to fail.
As the Bently Nevada 3500 (BN3500) protection cards have been declared obsolete by its OEM, card replacements are no longer available. AVR decided to replace the Bently Nevada system with a modern overspeed detection system: the Istec SpeedSys 200.
Challenge
Time was of the essence during this project, as downtime of the machine was costly to AVR. Therefore, Istec was required to deliver, engineer, implement, and commission the new system within a short period of time. Our engineers managed to do so within several days.
A second challenge was that there was no proper documentation available of the logical functions and trip philosophy of the overspeed detection system, beside the loop drawings. To be able to replace the former system and decide which (core) functions to take over, Istec needed to engineer the SpeedSys 200 configuration on-site.
Finally AVR wanted to keep using the existing 3-wire eddy current probes that were previously used to send speed signals to the BN3500 system. This raised two issues that required some custom engineering from Istec:
- The SpeedSys 200 is not designed to accept signals from 3-wire eddy current voltage sensors (only 2-wire current sensors).
- Bently Nevada eddy current probes require a negative supply voltage, whereas the SpeedSys modules expect a positive signal.
Solution
Istec has taken over all core functions of the BN3500 system in the SpeedSys 200 configuration.
Old system
The obsolete Bently Nevada 3500 system was configured with the following 19” cards:
- One 3500/50M tachometer module for zero-speed monitoring
- Three 3500/53M electronic overspeed detection cards
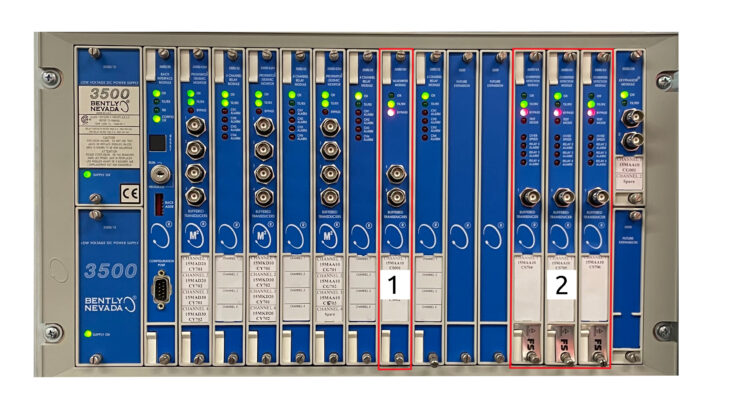
New system
By adding three GSI 127 galvanic isolators (one for each SpeedSys module) the existing speed sensors could continue to be used. The GSI 127 can reverse the signal of the eddy current probes to make it usable to the SpeedSys modules, while ensuring sensor monitoring remained available. Moreover, the GSI 127 units power the proximitor that is needed to generate output signals for the existing eddy current probes.
One of the relays of a SpeedSys 200 unit was configured to cover zero-speed monitoring, which was a function that was previously covered by the old BN3500 tachometer module.
The BN3500 was replaced with a 2oo3 SpeedSys 200 configuration. The DIN-rail assembly was engineered on-site and consists of the following components:
- Two 24V power supplies
- Three GSI 127 galvanic isolators
- Three SpeedSys 200 modules, hardwired to form a 2oo3 voting structure
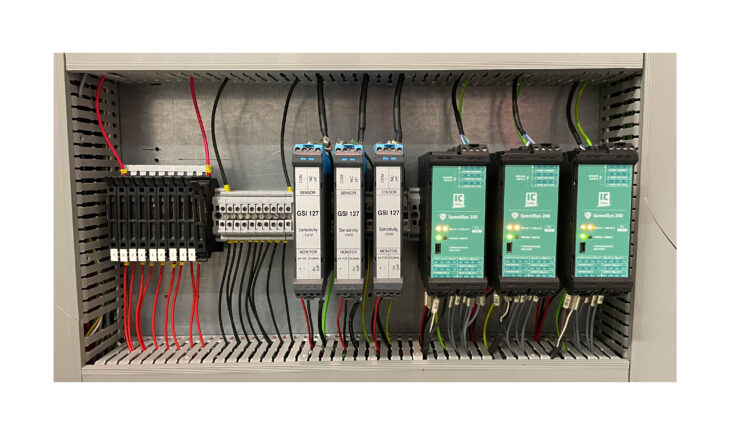
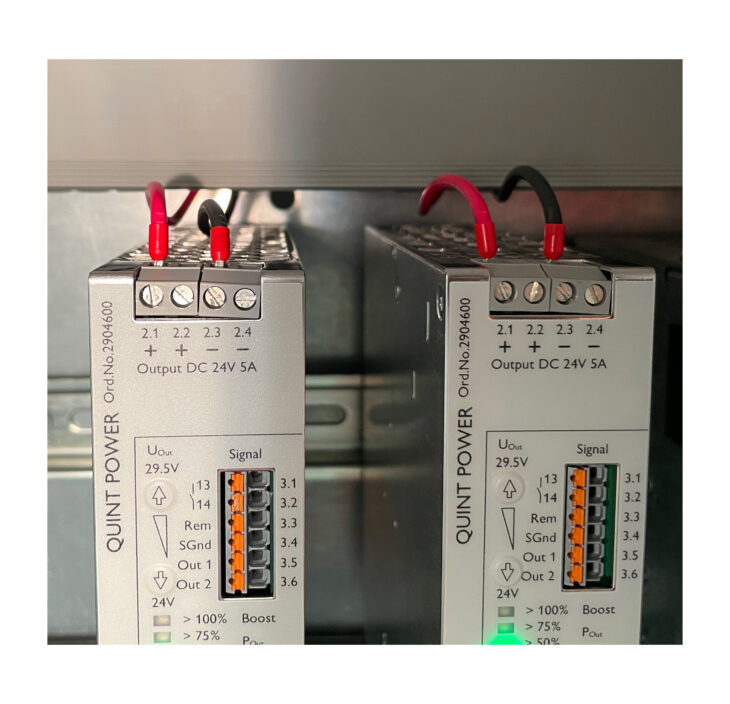
Deliverables
- On-site custom engineering to fit the new system in the existing infrastructure with minimal required adjustments
- Full scope supply and support of speed hardware and installation
- The SpeedSys replacement solution covers all of the core functions of the previous installation
- Fast troubleshooting, delivery, installation and commissioning
- The low-impact installation is SIL 2 certified by design, which allows for longer proof-test intervals than the previous system
Impact
Even though the engineering of the new system had to be done on-site, Istec has come up with a fast solution to replace the BN3500 cards with the SpeedSys 200 without the need for major infrastructural changes. The SpeedSys 200 installation covers all the core functions of the previous system. Any minor issues that occurred were quickly addressed and tackled by our team. With the help of Istec, AVR was able to start the turbine with the new SpeedSys 200 configuration just a few days after determining the malfunctioning the Bently Nevada overspeed cards.