It is very important that machines/installations in a factory are operational, especially when a factory needs to operate day and night. Unplanned downtime is highly undesirable, as it incurs high and unnecessary costs. Therefore, it is crucial to continuously monitor each machine, particularly the most critical ones, to prevent machine damage, which leads to (prolonged) unplanned downtime.
When there is a delivery obligation, this will also incur additional costs for the company. If a factory cannot operate for an extended period due to a malfunction or damage to a machine, the company cannot fulfill its delivery obligations. Although a significant investment in a monitoring system is required, it can make the difference between preventing a malfunction or experiencing one. Moreover, it greatly contributes to the safety of the employees, the factory, and the environment. A machine monitoring system operates autonomously; once installed, no one needs to interfere with it. This ensures the system is not susceptible to potential human errors, which are a major cause of industrial accidents.
An example
When a turbine goes into overspeed due to a malfunction, the consequences are disastrous if there is no monitoring system. When a turbine exceeds the maximum achievable speed, a monitoring system must intervene by shutting down the turbine. This happens when an alarm value is triggered, causing the monitoring system to shut down the turbine. Shutting down a machine is the last barrier before things actually go wrong. Often, other errors precede this that cause the turbine to go into overspeed. Examples of these errors include issues with the shaft, generator, or coupling.
Isolated layer of protection
The isolated layer of protection is the last barrier before things go wrong; the monitoring system shuts down the machine. To continue with the previous example; the gas turbine goes into overspeed and exceeds pre-set alarm values. The maximum number of revolutions per minute is exceeded, and the machine is immediately shut down. Before an isolated layer of protection intervenes, usually several steps precede it. One error leads to another until the alarm values are reached and the machine is shut down. In cases of overspeed, errors can occur so quickly that it is impossible for workers to intervene in time. The presence of a monitoring system that responds within 40 milliseconds (API 670 guideline) is therefore of great importance. The isolated layer of protection is never connected to a network (external) making it immune to cyber attacks.
Machine monitoring and condition monitoring
Machine monitoring systems are designed to ensure that the machine is shut down when necessary if a dangerous situation arises. This is often the result of a series of errors. Options for vibration measurements can provide a clear picture of the condition of a machine, often allowing intervention before alarm values are reached and the machine monitoring system trips.
An example
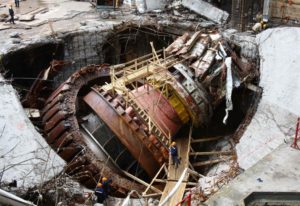
In 2009, a major accident occurred in a hydroelectric power plant in Russia (Sayano-Shushenskaya). Vibrations caused metal fatigue in the bolts that held the turbine’s valve in place. The bolts broke, causing the valve to come loose, and a large amount of water under high pressure to shoot into the generator room, causing extensive damage. 76 people died when the turbine in the hydroelectric power plant exploded due to vibrations. In addition to the victims, the hydroelectric power plant was responsible for an output of 6400 MW. For comparison; the largest energy plant (coal combustion) in the Netherlands has an output of 1560 MW. The sudden standstill of the entire hydroelectric power plant meant that the area was without power. The repair costs amounted to over 1.5 billion and took more than 5 years.
The metal fatigue caused by the vibrations could have been detected by a machine monitoring system (vibration monitoring). A machine monitoring system (with condition monitoring) is therefore of great importance. Even though the chance of something similar happening is very small, the consequences are unimaginable.
Machine monitoring for safety
Although unplanned downtime is always undesirable, a machine monitoring system can prevent severe consequences such as (fatal) casualties, environmental damage, and damage to the factory (and machines). The consequences of a turbine that is too susceptible to vibrations are unimaginable (as shown in figure 1). Besides the possibility of (fatal) casualties, the factory is so damaged that it will take months (if not years) to be operational again. This will cause severe financial problems and possible delivery issues. This concerns a hydroelectric power plant where there is a delivery obligation.
- Also read: The importance of predictive maintenance